薄板溶接を成功させるポイントまとめ
目次
薄板溶接とは
薄板溶接とは、一般的には1mm以下の母材に対して溶接をすることをいいます。溶接は原理的に母材を溶かして接合するので、板厚が2mm程度であればそこまで気にする必要はありませんが、1mm程度の薄板になると一般的な溶接方法として知られるTig溶接や半自動溶接では溶接範囲が広く必要以上に入熱しやすくなります。その結果、母材同士が接合される前に溶けて穴が空いてしまったり、熱が母材全体に伝わって歪みが発生してしまうなど、溶接の難易度が高くなります
薄板溶接の製品事例はコチラ >
なぜ薄板溶接は難しいのか?
金属同士を溶接するにあたって熱と歪みは切っても切れないもので、板厚が薄くなればなるほど難易度が上がります。なぜならば、溶接とは互いの接合部分を溶かして(溶けた部分をプールと言う)融合させますが、板が厚い場合は溶けたプール同士が付きやすいのですが、板厚が薄くなればなるほど母材のプールができる前に溶け落ちやすいからです。
また、薄板溶接では、溶接するだけではなく、溶接後の歪みをいかに少なくするかも重要です。溶接による歪が発生するメカニズムは、まず、接合部を溶融させる為に熱を入れる(溶接部は何千度にもなります)と母材が膨張し、その後、溶接が終わって冷えてくると逆に母材が縮小して元に戻ろうとする、つまり溶接の入熱による母材の膨張・収縮が発生するということがあります。さらに、溶接をしていない部分(熱影響があった部分とそうでない部分)に関しても発生する膨張・収縮に差が発生するので、最終的に歪が出てしまいます
板が薄くなればなるほど上記の影響を受けやすくなるので、一般的には溶接が難しくなります。しかし、溶接による入熱をコントロールすれば、上記のようなプールが抜け落ちたり、歪みが大きくなる等は回避することができます。
では、どういった工夫をし、治具を使えば薄板溶接でも歪みを回避できるのでしょうか?一般的には、①熱を逃がすために、溶接部に銅板を当てる②歪まないように治具で固定する③歪みが発生しにくいよう溶接の順番を工夫するという方法があります。
このように薄板溶接は難易度が高いため、機能上必要だがどうしても薄板の溶接ができないという理由で、①板厚を上げる、または②溶接をしない別の方法を採用する、ということが行われてきました。しかし、昨今では医療機器や電子機器、または自動車業界においては更なる軽量化・小型化などの目的で薄板へ溶接せざるを得ない状況になっています。そのため、穴を空けず、歪みなく、キレイに薄板溶接を行うか?という技術がますます求められています。
薄板溶接の種類と方法
薄板の金属同士の溶接と言っても、材質や板厚によって溶接方法は異なります。一般的に溶接には下図のような溶接式、溶接方法があり、この他にはスポット溶接などがあります。
まず、溶接の元になるアーク溶接について説明します。金属に流れる電流は電極間に多少の隙間があっても電流が流れます。このことをアーク放電と言い、アーク溶接はこのアーク放電の熱を利用する溶接方法です。
そして、アーク溶接は主に溶極式と非溶極式に分かれます。
①非溶極式・・・
電極自体はほとんど溶けずに、溶接棒を溶かすことで溶着する溶接方式
●TIG溶接
TIG溶接は電極に金属の中でももっとも融点の高いタングステンを使用し、不活性ガスをシールドガスとして使用する溶接方法です。特徴としては電極と母材の間にできたアークの中で溶接棒を溶かして溶接します。アークが安定しているのと溶融池が目視で分かる為、作業がしやすく綺麗な溶接ビードが出来ますが溶接速度が遅いという欠点もあります。
なおTIG溶接は熱伝導型の溶接になり、アーク熱を利用して母材を溶かし溶接する方法ですので、どちらかといえば浅く、広範囲の溶接に適しています。したがって、薄板などでは溶接範囲が広い為に穴があいてしまいます。
●YAG溶接
- YAG溶接は
- ・ イットリューム(Yttrium)
- ・ アルミニウム(Aluminum)
- ・ ガーネット(Garnet)
の頭文字をとってYAGといいます。YAGロッドを発振器とし、共振器というミラーに強い光を当ててレーザー光を発振させて共振器で増幅、強力な光の塊になりエネルギーを伝送します。小学生の時に理科の授業で実験したことがある方もいるかと思いますが、太陽の光を虫眼鏡に通して光を集約し、紙を燃やす原理と同じです。YAG溶接は熱が一点に集中する為、熱の入りが少なく、パルス制御なのでビードは均一でビード幅が狭くTIG溶接などと比較すると溶け込みが深く熱伝導も少ないです。
パルス制御による重ね照射の為、溶接ビードがうろこ状になりますが、熱伝導も少ない為、薄板溶接(t0.5程度まで)も比較的容易にできます。
●ファイバー溶接
ファイバー溶接はYAG溶接よりさらに進化したと言える溶接方法で、今一番注目されている溶接方法で、光ファイバーケーブルを使用した溶接です。余談ですが、金属母材を切断する加工機なども現在はファイバー切断が主流になってきています。
TIG溶接やYAG溶接はパルス発振による重ね照射の為、溶接ビードがうろこ状になりますが、ファイバー溶接は連続発振による連続照射の為、溶接部が滑らかで気密性が高く、溶け込みも深い溶接が出来る為、巣などの欠陥が少ない高品質な溶接が出来ます。また、熱源が光なので、電流や電圧などの影響が少ないのも特徴です。さらに、レーザー光がYAG溶接よりさらに小さく集約することが出来る(30~40μ)為、より局部加熱が可能で薄板、微細溶接(弊社ではSUS304 t0.05の溶接が可能)が出来ます。その為、医療、食品、化学等から非常に注目を浴びている溶接方法です。
また、ファイバー溶接は、異材同士の溶接も可能です。ステンレス+銅、ステンレス+ハステロイ、インコネル+プラチナなどなど多種にわたり溶接することが可能(弊社で実績あり)です。下の写真は弊社のファイバー溶接機で溶接したサンプルです。
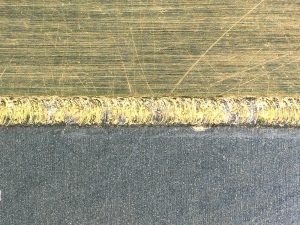
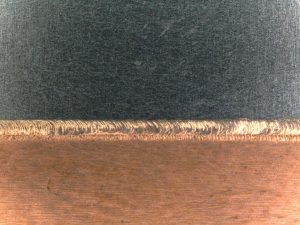
②溶極式・・・
電極自体が溶接棒の役割をし、溶極自体が溶けて溶着する溶接方式
●MIG溶接 MAG溶接 CO2溶接
溶極式の溶接方法の特徴は溶極自体が溶接棒の変わりになるという事です。溶極式にも複数の種類がありますが、一般的に屋内の工場などで使用されている半自動溶接機(CO2溶接)を代表として説明します。
半自動溶接機とはワイヤー供給器にあらかじめ溶接ワイヤーをセットし溶接ワイヤーとシールドガスを自動で供給します。作業者が溶接作業を行いますが、ワイヤー供給とシールドガスは自動供給の為、半自動溶接といわれています。溶接ワイヤー自体が電極となり、連続溶接が出来ます。その他のMIG、MAG溶接も使用するガスの種類などは違いますが、溶接方法としては同じです。TIG溶接や半自動溶接は共にどちらかといえば広範囲の溶接に適しています。
●セルフシールドアーク溶接
MIG、MAG、CO2溶接は溶接部にシールドガスを当てながら溶接をしますが、セルフシールドアーク溶接は、シールドガスを当てながら溶接はおこないません。なぜならば、セルフシールドアーク溶接は、電極である溶接棒自体に被覆剤が塗布してあり溶接時のアーク熱で被覆剤を分解することにより、シールドガスを発生させながら溶接をする為、溶接部を保護し溶接部の酸化も防いでくれます。主に屋外などではこの溶接方法が使用されています。
溶接には、いろんな種類がありますが、材質、板厚によって溶接方法や溶接棒も異なり溶接する材質、板厚によって使い分ける必要があります。
では、どの方法が薄板溶接に適しているのか?
ここまで説明してきたように、近年は溶接技術の進歩などにより、一般的なTIG溶接や半自動溶接のほかに、YAG溶接やファイバー溶接といったレーザー溶接など溶接方法も多様化しています。
YAG溶接やファイバー溶接には溶接ヘッドが固定式なっていて製品を台の上に置いて台を動かしながら製品を溶接する「固定タイプ」と、TIG溶接などと同じで手に持って溶接トーチを動かしながら溶接する「ハンディータイプ」があります。どちらも電流値など細かい調整は必要ですが、溶接職人のような技量などは必要としません。溶接速度も一定で行えるので、溶接もおこないやすく、溶接しやすい方法などを自分で考えることができれば女性でも十分溶接ができ、戦力となることが出来るのです。
いままでは、溶接=男性職人というイメージが強かったのですが、YAG溶接やファイバー溶接が普及してきたことにより、溶接に対するイメージが変わりつつあります。
では、薄板溶接に適した溶接方法とはなんでしょうか?
結論から申し上げると、薄板・微細溶接に適した溶接方法は、YAG溶接やファイバー溶接です。
それではなぜ、薄板溶接に向いているか?その理由を説明したいと思います。
TIG・YAG・ファイバー溶接簡略図
上図はTIG、YAG・ファイバー溶接の溶接径の簡略図ですが、TIG溶接は、タングステンを電極として使用している為、エネルギー密度が低く、溶接径が大きい為、広く浅い溶接になり瞬時に溶接材料を溶かす事が出来ません。したがって、母材を溶かすために余分に熱を入れる必要があり、熱が溶接材料全体に広がってしまい、場合によっては溶接母材に穴が空いてしまったり歪みが出てしまい製品にならない、あるいは歪み取りに苦労することが多くなります。よって、1mm以下の薄板や微細溶接は困難です。
一方、YAG・ファイバー溶接は、溶接径が小さくエネルギー密度が高い為、狭く深い溶接により瞬時に溶接材料を溶かす事ができる溶接方法です。YAG溶接は共振器というミラーに強い光を当ててレーザー光を発振させて増幅し、その強力な光の塊となったエネルギーをパルス発振して溶接を行う方法、またファイバー溶接は、光ファイバーケーブルを使用し連続発振による連続照射で溶接する方法です。
YAG溶接もファイバー溶接も熱源が光なので、電流や電圧などの影響が少なく、レーザー光をレンズによって1点に収束している為光を集約することが可能で、より小さな溶接径で局部を照射できるようになります。YAG溶接のレーザー径は一般的に200~400μ程度でありTIG溶接よりも入熱量も小さく済むので歪みを抑えた薄板溶接ができますが、YAG溶接ではSUSの場合t0.5程度の薄板までです。
その点、ファイバー溶接はYAG溶接よりさらにレーザー径が小さく集約できレーザー径は30~40μ程度になります。レーザー径が細いということは先ほども述べたとおり、より小さい範囲の局部溶接ができ、入熱量もYAG溶接以上に少なくなります。よって極薄板溶接や微細溶接が出来る様になるのです。当社のように薄板・微細溶接に特化していれば、SUSならばt0.05の極薄板も溶接が可能です。
ファイバー溶接では極薄板や超微細な溶接が出来る為、医療、食品、化学等など様々な分野から軽量化や曲げ及びプレスでは加工出来ないなどの困難な超微細加工も溶接にすることにより加工が出来る場合がある為、今非常に注目を浴びています。
チャレンジ!溶接の限界はどこか?
溶接に関して種類や方法などを紹介してきましたが、現在の薄板溶接の薄さの限界はどこなのか?疑問ですよね? という事でチャレンジしてみました。
サンプルとしてSUS304の極薄板に挑戦してみましょう!?
SUS304、t=0.05mm
上図はSUS304 t0.05同士の突合せ溶接を薄板専用の溶接機であるファイバー溶接機で溶接し50倍に拡大したものです。極薄板の溶接は電流の微調整や治具の製作が重要になってきますが、溶接ビード幅は・・・な、なんと0.136mm!です。極細のビード幅で肉眼ではただ線が付いている程度にしか見えません!。
(ビードの様子を詳しく見たいという方は、こちらをクリックしてください)ビード幅が狭いという事はその分熱の入りが少なくなる為、歪みや反りなどが軽減され薄板でも歪みの少ない製品を作ることができます。溶接は自動送りの為、溶接ビードも綺麗に出来ていますし、十分な気密性・水密性もあります!すばらしいですね。これならいろんな物の軽量化や微細な物にも対応できますね。
次にt0.03の溶接にチャレンジです!
SUS304 t=0.03mm
結果は、一見するときれいに溶接ができているように見えますが、100倍に拡大して見てみると・・・
うーん、、、板厚が0.02mmしか変わらないのに難しいですね。電流の微調整などを繰り返してもやはりt0.03mm同士の溶接になると難易度が上がります。なんとか溶接出来ている部分もありますが、このように目には見えませんが穴が空いてしまうこともあります。
極薄板の溶接は母材同士の密着性や切断面の精度にも左右されますがt0.05は溶接出来たのに、0.02mm薄くなるだけで溶接の難易度は何倍にも何十倍にもなります。たかが0.02mm、されど0.02mmの差なのです。極薄板溶接は0.01mmが生命線になってくるので奥が深く根気がいりますね。
現在の最新設備と技術でも、0.03mm厚の溶接は非常に厳しいのですが、今後こうした板厚にも対応していけるよう、薄板溶接.comでは技術開発を行っております。0.03㎜厚以下の溶接技術が確立した際には、お知らせしたいと思います。
薄板溶接の板金を成功させる為に、押さえておくべきポイント
ここまで溶接について述べて参りましたが、それでは、薄板を使った板金の製作を成功させるためには、どういった事を押さえておくことが必要なのでしょうか?ここでは「薄板溶接の板金を行うにあたり押さえておくべきポイント」と題して、設計や設備などの重要点をまとめておきたいと思います。
1 設計・データ
まず、薄板(微細)溶接を行うにあたり押さえておかなければならないのが設計です。設計・データの段階で7~8割は製品の出来が決まると言っても過言ではありません。それだけ重要なポイントになります。
なぜならば、設計・データを作る段階で後工程の曲げ、溶接方法の仕方も考慮して設計できなければ製品は出来上がらないからです。特に、薄板溶接はシビアさがより求められる(ex.t=0.05mmの場合なら、突合せ溶接部のクリアランスはほぼゼロになるように設計)上、歪みをできるだけ回避するために極力溶接を少なくすることも考え、簡単に加工出来るように設計しなくてはなりません。
2 切断加工
次に切断加工ですが、薄板溶接を伴う板金では、薄板をただ切断すればいいと言うものではありません。下の写真はSUS304 t0.3mmの板を弊社にある一般的なCO2レーザー加工機とファイバーレーザー加工機で切断し、直線部を20倍に拡大したものです。
①CO2レーザー加工機
②ファイバーレーザー加工機
-
③左 CO2レーザー 右 ファイバーレーザー 切断面合わせ
上記の写真を見ていただければわかる通り、①のCO2レーザー加工機で切断したものは、目視では真っ直ぐ切断出来ているように見えますが、20倍に拡大してみると波を打っているのがわかると思います。
一方、②のファイバーレーザー加工機での切断では、拡大しても切断面が真っ直ぐなのが分かると思います。また、③の写真のように、CO2レーザーとファイバーレーザーの切断サンプルの2枚の切断面を突き合わせてみると、切断面と切断面の間に隙間が出来ているのがわかります。
実は、薄板(微細)溶接をするにあたってこの隙間が非常に重要で、コンマ何ミリの隙間がある為に溶接がうまく出来ないことは、薄板溶接ではよくあることです。したがって、薄板を綺麗に真っ直ぐ切断することが後工程で非常に重要になってくるので、薄板切断専用のファイバーレーザー加工機でさらに最適な切断条件を調整し切断を行う必要があります。
3 曲げ加工
薄板(微細)溶接板金を成功させる次のポイントは曲げ加工です。設計、切断で製品になる物もあれば、切断後、曲げなしで溶接するものや曲げ加工後溶接するものなど様々なパターンがありますが、切断後、曲げ加工なしで溶接工程にいく製品は意外と少なく、例えば薄板溶接.comを運営する㈱マツダで扱っている薄板(微細)製品の場合、8割以上の製品が曲げ加工を含んでいます。お客様からの支給部品で溶接のみは別として、薄板(微細)溶接を行う製品は、基本的には板厚0.1t~0.3tなどの極薄で製品サイズも手のひらサイズの物が多い為、一般的な曲げ加工で使用するプレスブレーキの金型で曲げることができないものが多くあります。
●薄板溶接は、精密な曲げ加工技術が求められる
薄板溶接では溶接個所の板と板の密着度が重要になります。例えば、SUS304の板厚0.1mmの板を四方曲げして箱を作った場合、角の板同士の合わせ面の隙間が0.5mmも開いてしまうと薄板(微細)溶接は出来ません。この溶接部の隙間(密着度)が溶接の可否に大きく関係する為、曲げ精度(隙間など)不足ということで次工程に進めず、製品がNGになることもあります。以上のことから曲げ加工はただ曲げればいいということではなくとても重要な位置付けになります。
4 治具
次に薄板(微細)溶接を行う次のポイントは治具の製作です。薄板(微細)溶接は前述の通り、設計から始まり、切断、曲げなど含め前工程が非常に重要で、高い精度が求められます。それに加え溶接時のセッティングについても、押さえ方によっては変形してしまったり、人の歩いている振動でさえ溶接に影響してしまったりするほどシビアなのです。その為、溶接をしやすいように治具などを考え固定したほうが溶接はしやすくなります。
ピンセットや極小の精密ドライバーなどはもちろん、すべての溶接面が平面ではない為「角度を変えて溶接できる角度治具」、薄肉パイプ類などを回転させながら溶接を行う「回転治具」など製品によって溶接の仕方も変わるため、あらゆるものを応用して治具を考える必要があるのです。
5 溶接加工
薄板、微細溶接は前述の条件をすべて満たしていることが最低条件になります。そのうえで薄板(微細)溶接を行う際のポイントは、溶接方法です。
一般的なt0.5mm以上であればTIG溶接やYAG溶接で十分に溶接することができると思いますが、それ以下の極薄板では今までの常識は通用しません。一般的には薄板を溶接せずに、プレス加工や絞り加工、または板厚を厚くするなどの対応が必要になってきます。しかし、プレス加工にしても製作数1~2個で行うのは金型代などの費用面からも難しく、また軽量化を目的にしているので板厚を上げられないなどの、様々な問題があります。
しかし、近年では極薄板溶接が可能な溶接機があります。それは、ファイバー溶接機です。ファイバー溶接機はガラスファイバーを使用し光を熱源とした溶接方法です。
ファイバー溶接機の特徴は、局所加熱、ビーム径が非常に小さくエネルギー密度が高い為、細く深い溶け込みが出来ること、熱による歪や変形、溶接焼けなどが少なく出来ることが特徴です。また、ビーム径や出力が調整できる為、融点が異なる材料(異材溶接)など様々な溶接をすることが可能です。ただ、すべての金属を溶接することが出来るわけではありません。
最後に
薄板、微細溶接は前述のとおり、薄板溶接をふまえた設計から始まり、切断精度や曲げ寸法(溶接面の密着度)の精度などすべてが揃わなければファイバー溶接機であってももちろん薄板溶接は出来ませんし、すべてのファイバー溶接機が同じように薄板溶接が出来るわけではありません。ファイバー溶接機にも出力の違いや薄板溶接に向き不向きなどがあり、それぞれの溶接機には様々な特徴がある為、薄板溶接するのに適した溶接機にて、条件出しや知識、経験を身につけることが必要です。
以上のことをふまえてようやく薄板(微細)溶接が可能になります。